Have you ever enjoyed a day at the beach having to carry your chair, umbrella, and cooler; only to struggle with dragging your cooler across the sand because the wheels are digging in?
On a much larger scale, this was a major dilemma for the Seabees when it came to their ship-to-shore responsibilities of getting troops, their equipment, and vehicles off ships, across pontoon causeways, and on to a beach. This concept is also known as an amphibious landing.
The ability to move heavy vehicles and equipment across the short distance from a landing craft ramp or pontoon causeway to solid ground was crucial to the success or failure of a landing force in gaining a foothold on the enemy shore.
One of the complications connected with amphibious landings during WWII involved moving heavy equipment across mushy beach sand. Tires mired in and cut deep ruts in the sand, stalling equipment and making some exits from the beach impassable.
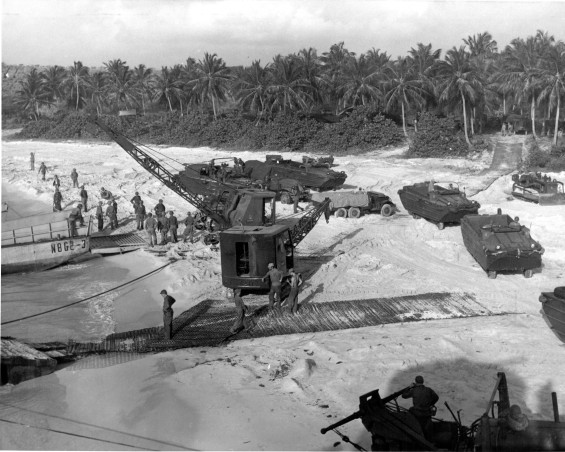
Seabees bringing supplies off a pontoon causeway onto a beach landing using Marston Matting and DUKW’s (“Ducks”). (U.S. Navy Seabee Museum Archives)
Two amphibious vehicles- the amphibious tractor and the DUKW (also known as a “Duck”) were designed to overcome these complications, and were relatively successful. But even equipment with sufficient traction to plow through the soft, spongy earth was slowed down, greatly increasing the time required to get supplies ashore.
The question came down to this: How to achieve a hard beach surface in minimum time, at minimum cost, with minimum equipment and personnel, and with material which would not be in critically short supply during war time?
One of the creations during the war to overcome this obstacle was called Marston Matting, also known as Pierced Steel Planking or PSP. It became the standard steel matting utilized by the Seabees to construct not only sand beach landings, but also to build airfields and temporary roads.
It got its name from the town of Marston, NC where the invention, by a Pittsburgh steel specialty engineer named Gerald G. Greulich, was tested.
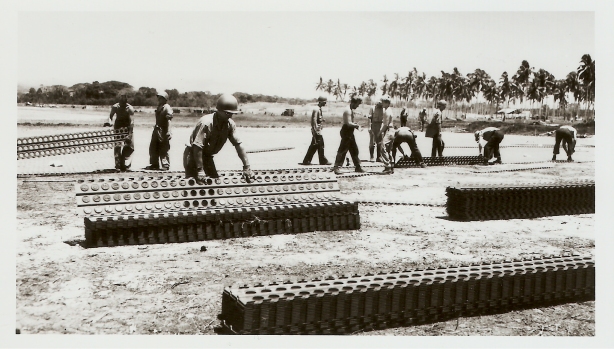
Marston Matting being quickly assembled to construct an airstrip in the Pacific Islands. (U.S. Navy Seabee Museum Archive)
Marston Matting had many advantages. A single piece measured 10 feet long and 15 inches wide. The hole pattern for the sheets was 3 holes wide by 29 holes long resulting in 87 holes per plate. The circular holes allowed the planking to be laid on top of a surface that has been roughly graded.
Marston Matting allowed rapid construction; it was pre-fabricated and fit together quickly. It was lighter and required less cargo space than other matting, and could be used in all-weather conditions because it was highly resistant to corrosion.
Seabees were fond of Marston Matting because it enabled them to do their jobs quickly and efficiently.
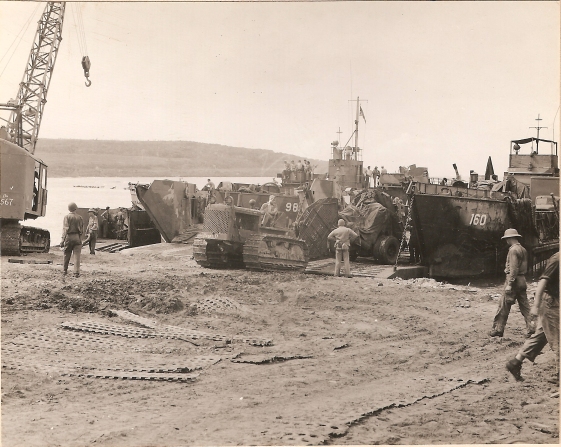
Amphibious landing utilizing Marston Matting to move heavy machinery across the beach. (U.S. Navy Seabee Museum Archives)
Often, Seabees were subject to enemy fire while laying down the matting. The benefits of using this matting were substantial when in the course of it being subject to enemy fire and destroyed as a result, the sectional matting could be quickly replaced.
The creation of Marston Matting helped the Allies transport their equipment faster from ship-to-shore, build roads on any terrain necessary and fastened together quickly to construct airstrips. It gave the Allies an advantage in Normandy on Omaha Beach, and throughout the Pacific Theater.
Marston Matting helped win the war.
——–
Meet the Curator: Robyn King
Robyn King earned her Bachelors in History and Anthropology from the State University of New York at Oneonta. She has experience working at State Museums, Historic Sites, the National Parks Service, and most recently the Navy. She’s an expert in collection management, and has worked closely with both natural and cultural collections. Robyn loves all museums and sharing her love of history. When’s she not working, she’s volunteering her time with the National Peace Corps Association, as a Returned Peace Corps Volunteer from West Africa.
[…] landing and operability of equipment on the sandy beaches. This required the rapid placement of marston matting that allowed for machine operation on the beaches, a vital tool which was noted as one of the […]
LikeLike